8 Common Mistakes to Avoid When Using Industrial Scales
- dcolston
- Jan 30
- 5 min read
Updated: Feb 21
Using industrial scales is crucial for accuracy in measurement, but many users fall into common traps that can lead to errors. In this post, we’ll explore those mistakes to help you achieve optimal performance and precision in your weighing tasks. Let’s dive into the most frequent pitfalls!
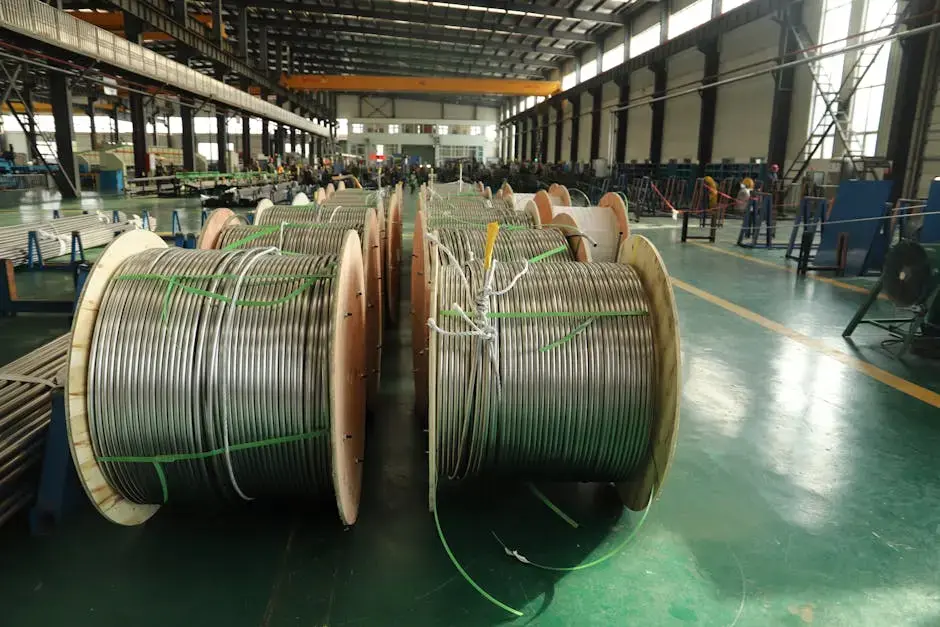
1. Neglecting to Calibrate Regularly
Calibration is essential for accurate readings. Learn why skipping this step can cause significant discrepancies. In the realm of industrial scales, neglecting regular calibration can have serious consequences. Over time, equipment naturally drifts out of alignment due to wear and tear or environmental changes. Even minor discrepancies, if not addressed, can escalate into major errors, impacting the quality of your measurements. Consider implementing a routine calibration schedule to counter these effects. This ensures that your scale not only maintains its accuracy but also extends its operational lifespan.
It’s not just about saving money; it's about maintaining the integrity of your work. Think of calibration as a necessary check-in that keeps your scales in peak condition. By doing so, you assure yourself that every measurement taken is dependable, which is crucial in many industrial applications. Trust in your tools will undoubtedly lead to greater confidence in your findings.
2. Ignoring Environmental Factors
Temperature, humidity, and vibrations can all affect measurements. Understand how to mitigate these influences. Environments that are too cold, too hot, or overly humid can skew your results significantly. For instance, when a scale is introduced to fluctuating temperatures, it can expand or contract, resulting in erroneous readings. Hence, ensure your scales are kept in a controlled environment wherever possible. Use climate control systems if your workspace isn’t naturally stable.
Moreover, vibrations from nearby machinery can cause the scale to register false readings. If your scales are near such sources of disturbance, consider implementing vibration dampening techniques. A simple rubber mat can often do wonders in minimizing these disruptions. Remember, your physical surroundings play a powerful role in the performance of your industrial scales.
3. Overloading Industrial Scales Beyond its Capacity
Exceeding the weight limit can damage your scale and lead to inaccurate readings. Find out how to choose the right scale for your needs. Each industrial scale is designed to handle a specific weight limit, and exceeding it can not only yield false readings but can also lead to permanent damage. When investing in an industrial scale, assess your maximum weight requirements thoroughly. It's advisable to select a scale that exceeds your anticipated load to provide a buffer zone.
This foresight will save you from unnecessary headaches down the line. Furthermore, educate your team about the scale's limitations, ensuring everyone understands how to operate it safely. Regular reminders about the importance of adhering to weight limits can maintain the reliability of your equipment and improve workplace safety.
4. Failing to Use the Right Weighing Technique
Different scales require different techniques for accurate results. Learn the best practices for using your industrial scale. It's essential to familiarize yourself with the specific method that best suits the type of industrial scale you are using. For instance, when using a balance scale, it’s crucial to place items in the center of the weighing platform. This ensures that your readings are consistent and precise. On the other hand, using load cells often necessitates a more dynamic approach.
Investing time in training your staff on these varying techniques can yield far better accuracy and reliability in your measurements. Remember, effective weighing is not just about the equipment; it's also about the personnel behind it. Adopting proper techniques leads not only to better data but also enhances the overall efficiency of your industrial processes.
5. Neglecting Proper Maintenance and Cleaning
Dust and debris can affect performance. Discover cleaning tips to keep your scales in peak condition. Much like any piece of equipment, industrial scales require regular upkeep to perform at their best. A buildup of dust, dirt, or spills on the weighing surface can significantly affect your readings. A quick daily wipe down can prevent larger issues from arising. Use a microfiber cloth or a soft brush to clean sensitive areas without damaging the scale.
In addition to regular cleaning, another aspect of maintenance involves checking for any visible wear and tear. Small cracks or signs of rust can indicate that your scale could use some professional servicing. By staying on top of both cleaning and repairs, you can ensure that your industrial scales operate efficiently for years to come.
6. Rushing the Weighing Process
Hastiness can lead to errors. Understand the importance of taking your time for precise measurements. In the fast-paced world of industry, it may feel tempting to rush your weighing process to keep up with demands. However, hurrying can compromise accuracy. Taking a moment to ensure that your load is stable and centered on the scale will yield far more reliable results. Rushing invites mistakes that could cost you time and money, something no one can afford to overlook.
Encourage a culture of patience within your team. Implementing a checklist to guide the weighing process can serve as a reminder for everyone to slow down and take their time, promoting not only accuracy but also mindfulness in the workplace. Quality should always trump quantity in measurement practices.
7. Using an Unstable Surface
A level and stable surface is crucial for accurate weighing. Explore how to set up your scale correctly. Have you ever considered the impact of your scale’s placement? An unsteady surface can dramatically alter the accuracy of your measurements. Ideally, your industrial scales should be placed on a flat, sturdy surface. If the ground is uneven, even slightly, it can throw off the readings, leading to costly errors.
Consider using leveling feet or a leveler to fine-tune the setup. Regularly check for stability and make adjustments as needed. A firm foundation not only enhances accuracy but can also prolong the scale’s lifespan by preventing undue stress on mechanical parts.
8. Not Training Staff on Proper Use
Inadequate training can lead to misuse. Learn how to ensure your team understands the correct procedures for operating industrial scales. One of the most significant factors influencing the performance of your industrial scales is the expertise of the operator. If your staff isn’t well-trained on the specifics of how to use the equipment properly, even the finest scales can yield subpar results. Comprehensive training programs can help bridge this knowledge gap.
Include hands-on training sessions and detailed manuals outlining procedures and best practices. Holding periodic refreshers can also help reinforce this knowledge. When your team understands how to use the scales correctly, you're not just preventing errors; you’re also fostering a sense of accountability and pride in their work.
Comentarios